An Interview with Kevin Copleston, one of the founders of Sensor Solutions Ltd
Crack detection and crack propagation sensors are two different things.
Say you’ve got an aircraft structure and you’ve got two components riveted together. These are the typical weak points, cracks often propagate out from this type structure.
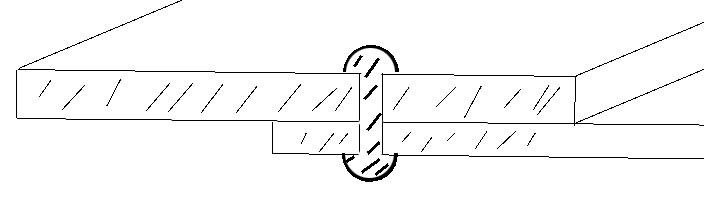
The first thing you can do is crack detection.
That is a gauge that looks like this, if you’ve got a rivet you’d put it there, if a crack comes out it would then break this. It’s made like a strain gauge.
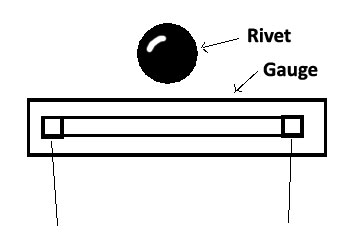
Sensor Solutions: ‘It’s a bar basically.’
Yes it’s a bar, it’s a very thin, it’s in intimate contact with the stuff, brittle backing and if a crack gets this far, there very cheap that’s the thing, crack detection is cheap, these are pennies.
If it breaks that you get open circuit, oh! I’ve got a crack. Ah, is that crack critical?
Is it critical? Have we got more than one crack? No hang on this is critical, it’s out of our.., it’s at a critical juncture.
If it is critical, how fast is it migrating? Then we have to use something called a ‘crack propagation gauge’.
Crack Propagation Gauges
Diagram of a propagation gauge:
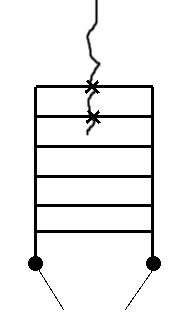
These gauges are far more complex, they are not a simple circuit.
The illustration is a simplified diagram, it’s actually more dense than that, and there’s two types.
For static, or slow dynamic change, for instance on aircraft airframes:
With these, you connect them and measure the resistance across this gauge in the same way you do with a strain gauge.
What happens is the propagating crack comes along, it breaks that run, resistance goes up in a step.
If the crack continues more runs are broken, with resistance stepping up every time.
So you’re looking at the step change, you can measure the rate of propagation of the crack.
So if you have a crack you’d put the sensor on and there and see the rate of change.
With aircraft, they look at the rate at which the crack is propagating. They will apply a patch. They will do a fix, drill a hole at the end and put a patch over it the crack and rivet that on. Then you’d fly it and see if that crack reinitiates and propagates again, or whether you’d cured it.
If you’ve cured it, good, at the C2 check the plane comes in, you know exactly where the crack’s going to be, then a validated repair happens, job’s done.
For crack propagation in the understanding of materials:
This has a completely different approach. You have a sample, you put a V in it and you would apply a shock load to it, and you’d snap it.
You’re interested in the rate of propagation over very fine increments, you’d use a gauge that looks like this:

Sensor Solutions: ‘So you’re going to measure the speed of crack propagation? A test happens and you measure how rapidly that crack propagates?’
Yes, how quickly it propagates, and you get many, many, runs in there.
This is because you are looking at, instead of big increments, what happens over a couple of millimetres, you’ve now got 20 runs to the millimetre. It’s finer than the aircraft propagation strain gauge.
There’s no initial crack in there, but you’d put a stress concentration on it, you’d load it
The test piece would load, load, load and then ping!
You want to understand what happens, it could trying to understand the way you roll the material, the type of material, or if it’s a composite, whether the fibre direction works, that sort of stuff..
You are doing material science rather than structural science and these are much finer increments and they tend to be logarithmic until failure.
So same sort of measurement technique but much faster.
Crack detection is cheap, crack propagation is not so cheap it’s quite dear.